简介:
近日,由中国海洋石油集团有限公司自主设计建造的世界最大桁架式半潜平台组块在中国海油青岛场地完工装船,标志着我国深水海洋工程装备自主设计建造技术和能力水平进一步提升。据了解,此次建造完工的组块是全球首个
近日,由中国海洋石油集团有限公司自主设计建造的世界最大桁架式半潜平台组块在中国海油青岛场地完工装船,标志着我国深水海洋工程装备自主设计建造技术和能力水平进一步提升。
据了解,此次建造完工的组块是全球首个万吨级半潜式储油平台的重要组成部分,由23个甲板片组成,装配近200套关键油气处理设备,并包含一个可以容纳120人的生活楼;设计重量近2万吨,相当于近200辆超重型卡车的载重量总和;敷设电缆总长达43万米,可环绕北京六环两圈多。
“与传统的箱体式半潜平台组块相比,桁架式结构具有重量轻、钢材用量少等突出优点,但存在受力计算复杂、疲劳性能要求高、重量控制和精度控制挑战大等困难。”海洋工程陵水17-2气田开发总包工程项目副总经理韩少宁说,作为国内首个应用于1500米深水高压气田的组块,其工艺流程和油气处理系统也是国内现有海上油气平台中最为复杂的。
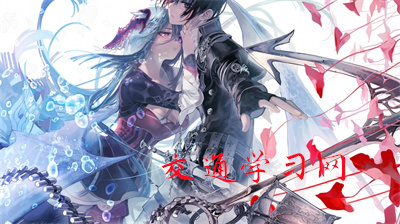
据陵水17-2项目上部模块部经理刘新宇介绍,项目首次大规模应用了超高强钢,对材料控制、焊接工艺、焊工技能等都提出了更高的要求。主立柱间最大跨度达到50米,公差不得超过普通铅笔的直径,这在整个行业都是最严格的。此外,项目首次建造了板壳式生活楼并大面积使用成品支吊架,加上专业交叉密集、吊装合龙干涉多、施工周期短等难题,为项目实施带来了极大的挑战。
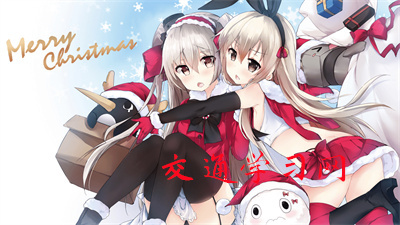
自2019年5月项目开工建造以来,项目组搭建了五级网格化组织机构,建立了风险控制、精度控制、重量控制等多个专项工作组,通过封闭式、强矩阵、精细化管理和可视化工程项目管理系统等信息化工具应用,显著提升了组织和施工效率。在各方密切协作下,项目团队集中优势资源,优化建造方案,完成十多项施工技术及管理创新,并成功克服新冠肺炎疫情、持续强对流台风天气等诸多因素影响,高峰时期组织1500人昼夜奋战,在确保质量安全的同时,仅用17个月便完成了组块建造工作,用实际行动展示了“中国速度”。